How to operate and learn CNC EDM fixture tool system for mould making
HPEDM’s precision fixture system is divided into three major systems: CNC positioning system, EDM positioning system, zero point positioning system.
HPEDM has divided precision fixtures into three categories. Which make it easier for users to quickly find their requirements.
Kindly check the The following several systems.
The EDM positioning system has a large similarity with the CNC positioning system, but the application of machining centers is not the same.
EDM positioning system: As the name implies, it is the precision fixture commonly used in EDM processing. It is generally worthy of a precision fixture system for spindles;
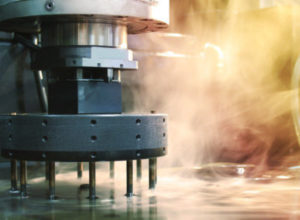
CNC positioning system is a precision fixture system for CNC machining center worktables. Both of these systems consist of similar parts. The constituent elements include the following aspects:

- Chuck. The chuck is the most basic part of all positioning systems. Without a chuck, the system cannot operate. If you want to use the EDM positioning system, you must have a round or square head chuck for the spindle; a CNC machining center must have a single or multiple table chuck. The difference between the chucks of these two systems is that the location used is not the same.
2, electrode holder: It is a tool that holds the electrode or workpiece directly. Choosing the right chuck and holding the electrode will help improve the yield of product processing.
- The positioning plate is the main source of the accuracy obtained by the entire system. The line contact between the positioning plate and the positioning ridge of the chuck leads to flexible deformation and provides positioning accuracy of ±0.002 mm.

4, system accessories. This includes parts or replacements that maybe used in the positioning system. Such as pull nails, pull ring, anti-chip aluminum plug, valve switch and so on.
5, measure tool. Whether it is EDM or CNC machining, the chuck needs to be scored during the first processing. The presence of the detection element is to make the sub-inspection easier and more convenient.
6 wire cut EDM machine system. Wire cutting is one of the EDM processes and is unique to the EDM positioning system. Use wire cutting fixtures to make WEDM easier to process and more precise.
The above part constitutes the EDM positioning system and the CNC positioning system. The system seems to be more complicated, but it is also the system make it is possible to achieve rapid change-over and provide high-precision production.
The zero point positioning system can keep the workpiece from one station to another station, from one process to another, or from one machine tool to another. The zero point always remains unchanged. In this way, the auxiliary time for re-aligning the zero point can be saved, the continuity of the work can be guaranteed, and the work efficiency can be improved.
HPEDM fixture system is subdivided so as to promote the rapid positioning of fixtures and give customers a new choice. Hopefully, you will not only know about the fixture system but also how to understand and operate the precision fixture system.

We specialize in all kinds of CNC EDM tool . air chuck , manual chuck , self centering vise , EDM brass electrode holder, EDM pneumatic chuck , wire cut vise, wire cut clamping beam.
Most of our products can compatible with EROWA , 3R tooling system.
Repeatability: 0.002mm. Good price to help you save much cost and time.
Web: www.cncedmtool.com